REFERENCES
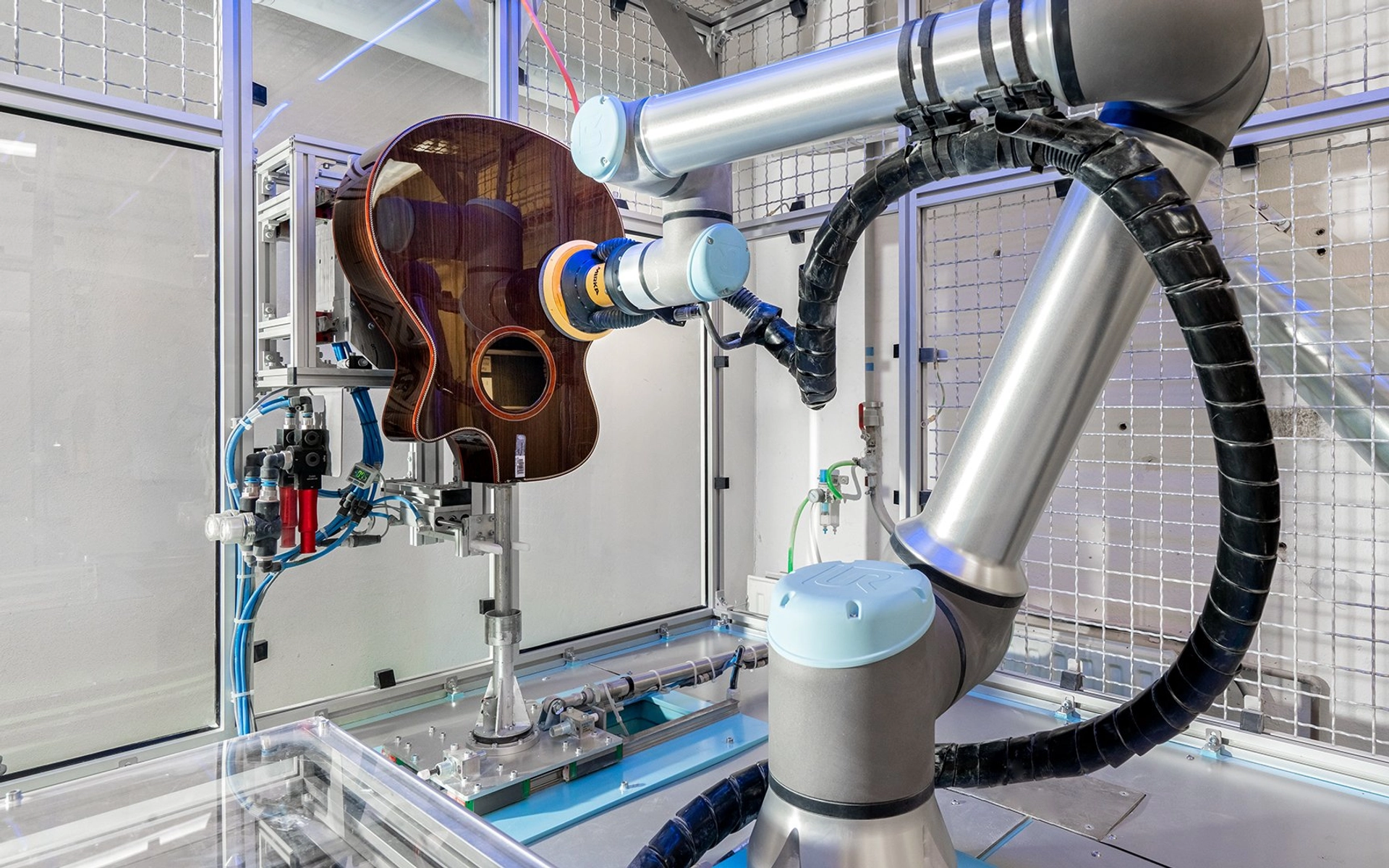
FURCH GUITARS - ROBOTIC CELL FOR INTERLAYER SANDING OF UV CLEARCOAT
WORKPLACE
At the workplace at Furch Guitars, we installed a Universal Robots UR10e six-axis collaborative robot equipped with a Mirka® AIROS 650CV sanding head with integrated dust extraction. The workplace offers two workstations for two guitars, so that continuous deployment of robotic sanding is possible. The robotic arm sands the first guitar and then moves to the sanding position of the second guitar. During the sanding of the guitar in the second position, the operator changes the guitar in the first position and conversaly.
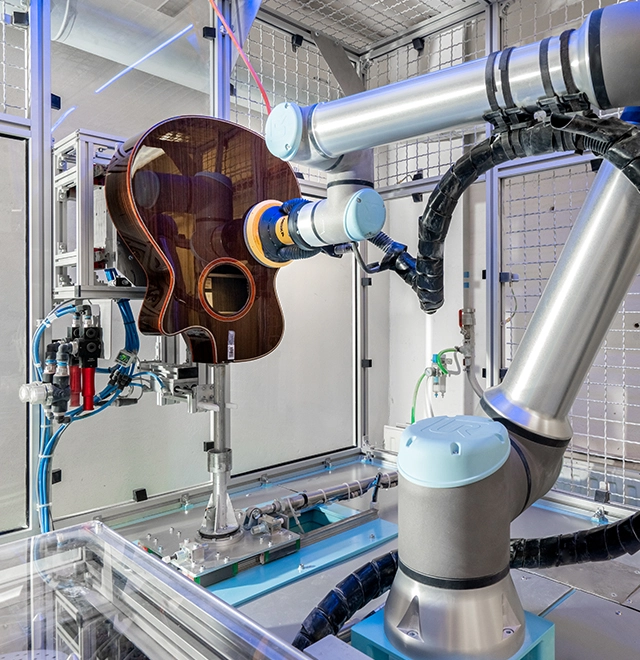
FUNCTION
A mandrel is used to fix the guitar at the sanding workplace, on which the guitar is already fixed during fully automatic painting. The mandrel is placed in a bed in the sanding cell, and the guitar itself is additionally fixed on the unground side by a pull-out table with suction cups (vacuum).
An interesting feature of the workplace is the colored LED RGB lighting, which replaces the classic status traffic lights common in industrial workplaces. In the event of a detected error or sanding interruption, the entire workplace is illuminated in red. If everything is in order, the workplace is illuminated in blue. Thanks to the use of LED technology, the color can be chosen according to the customer's request.
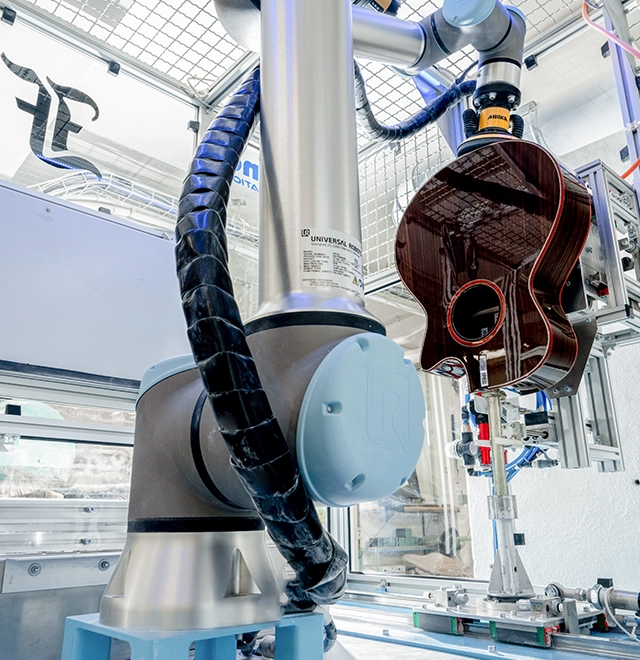
ABRASIVE
Due to their high hardness, Mirka Iridium abrasive is used when sanding the interlayers of UV topcoat. The abrasive is placed in the reservoir of the automated exchange unit, which is integrated inside the robotic sanding cell. According to the given program, the robotic arm selects and attaches the appropriate abrasive to the velcro of the backing pad of the sanding head. The worn abrasive is removed from the backing pad again in the automated abrasive exchange unit and falls into the appropriate box for used abrasive.
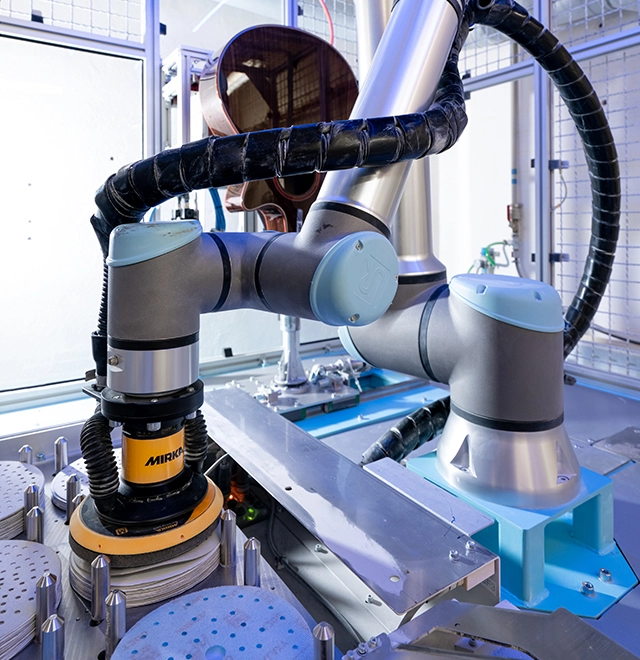
FURCH GUITARS - ROBOTIC CELL FOR SANDING GUITAR BODIES BEFORE PAINTING
WORKPLACE
The workstation used by Furch Guitars for sanding acoustic guitar bodies before painting is equipped with two six-axis collaborative robots from Universal Robots. Thanks to the universal gripper, the handling robot UR5 ensures that ten different types of guitars are mounted on a unique rotating clamping table, which not only clamps the guitar, but also centers it in the desired position, needed for sanding. Reliable fixing is ensured by the vacuum generated by the vacuum cleaner. The second collaborative robot UR10e is used for sanding itself and is equipped with a Mirka® AIROS 650CV sanding head with integrated suction. At the given workplace, the body of the guitar is ground completely from all sides, including the so-called lobs (sides).
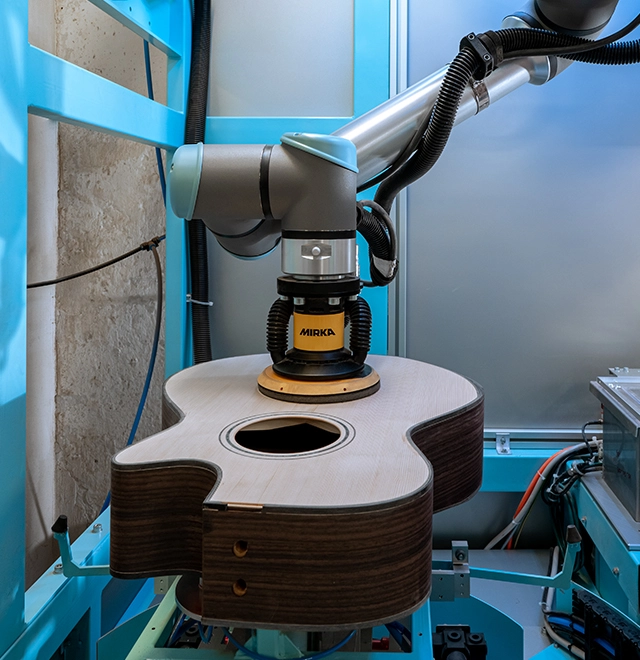
METHOD
After the sanding operation is completed, the guitar body is placed in a storage box, from where the guitars are taken by the production operator.
The workplace uses, as in the previous case, colored LED RGB lighting, which not only illuminates the workplace, but also serves as a signal of the status and progress of robotic sanding.
Mirka Gold abrasive is used for the given sanding operation. The abrasive is again placed in the automated abrasive exchange unit, integrated inside the robotic sanding cell. Here, according to a predefined program, the robotic arm selects and attaches the abrasive to the backing pad of the sanding head. The worn abrasive is removed from the backing pad again in the automated abrasive exchange unit and falls into the appropriate box for used abrasive.
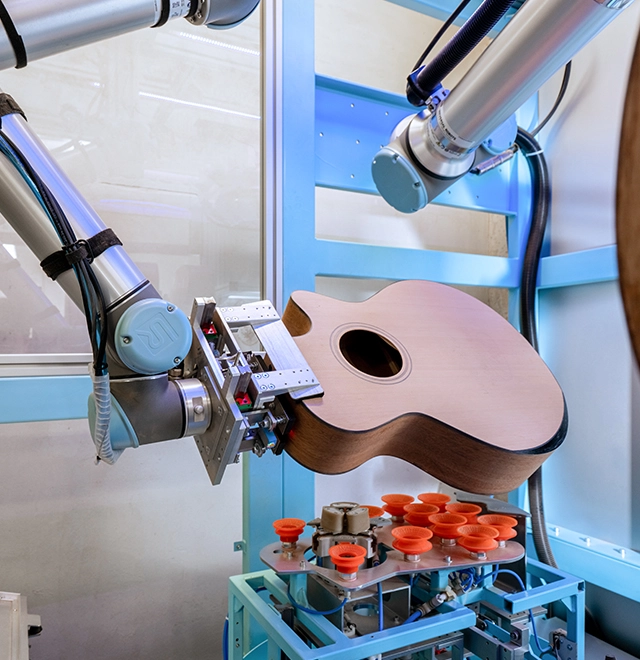
INCOSYSTEMS - UNIVERSAL ROBOTIC CELL FOR SANDING CARBON PARTS
FUNCTION
The workplace implemented at INCOsystems is used for sanding raw carbon parts before the filler and their subsequent sanding of individual layers after the application of special fillers and coats for the surface treatment of carbon parts. The cell is primarily intended for sanding carbon car roofs. However, thanks to the variability of the clamping, it can also be used on other carbon products, such as various exterior aerodynamic elements, as well as interior parts made of carbon.
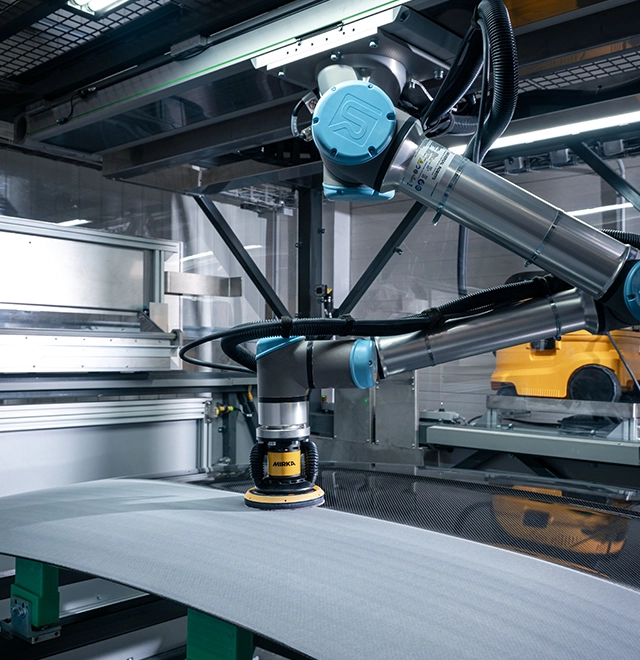
METHOD
The sanding part is placed outside the robotic cell on a loading handling trolley, which can be customized to hold different shapes and types of parts. After the part or parts have been fixed, the operator slides the cart into the robotic cell, where the robotic sanding itself is then started.
Our solution is based on the six-axis robotic arm of the UR10e collaborative robot, which is extended by a seventh travel axis, anchored to the ceiling part of the workplace structure. The robotic arm is fitted with a Mirka® AIROS 650CV sanding head.
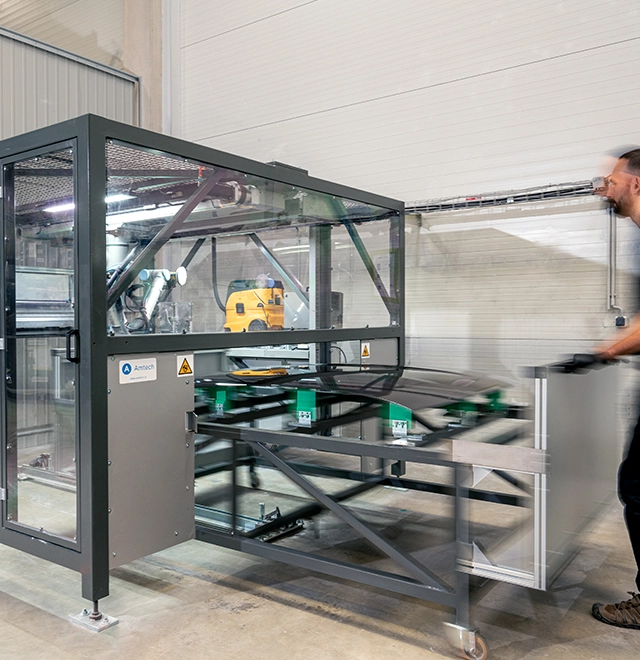
ABRASIVE
Sanding at this particular workplace uses Mirka Abranet net abrasive, which is characterized by excellent dust extraction and long life. The selected program selects the correct abrasive coarseness for the given sanding operation from the automated abrasive change unit. The used abrasive is removed from the backing pad again in the automated abrasive exchange unit and falls into the appropriate box for used abrasive.
At the additional request of the customer, the workplace will be equipped with LED RGB strips for signaling the status of the process, as was described in the solution for the Furch company.
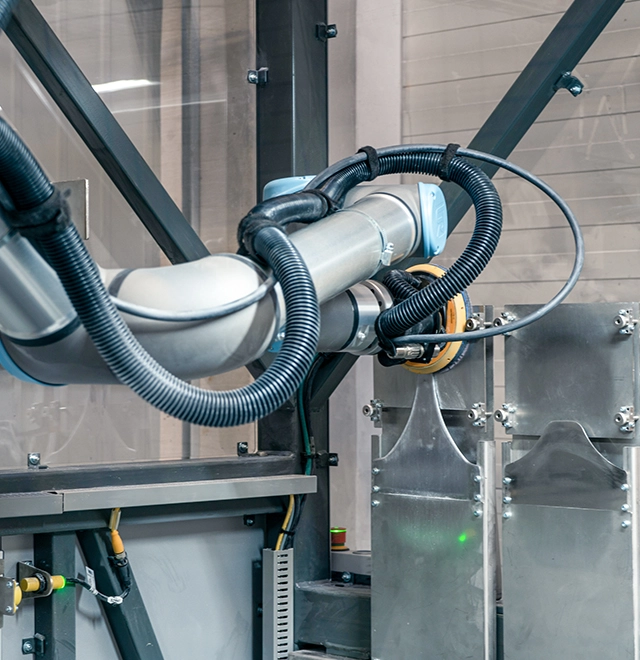